Mineral Wool (MW) panels have different characteristics to other core type panels. One of these differences is in handling and storage of panels on site. Installation crews may be very experienced with traditional insulated panels however some of the practices used for handling these panels are UNACCEPTABLE when handling MW panels.
Watch this helpful video to learn the correct method for handling and installing MW panels.
Site Storage of panels
Upon delivery to site the packs of MW panels must be stored on a flat, level and stable surface, preferably concrete
Packs of MW panels must be stored to ensure the panels do not get wet. The factory wrapping may not be adequate to ensure the panels remain completely dry so additional protection should be used, preferably store the panels indoors.
When lifting packs of MW panels by forklift always lift at the marked lifting points.
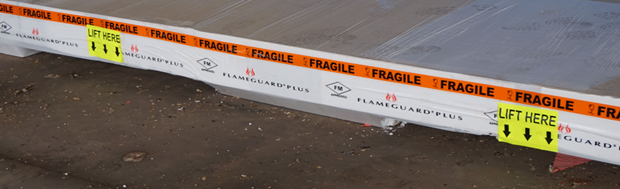
Separating the top panel from the stack
When separating the top MW panel from a pack of MW panels one end of the panel should be slid slightly to one side of the pack. This enables workers to lift the end of the MW panel by gripping under the bottom skin of the panel.
Never lift a MW panel by the top skin only.
Lifting equipment
Selection of the correct equipment to lift and install the MW panels is dependent upon several factors;
- Length and thickness of the MW panels to be lifted,
- Landing location of the MW panels above/below floor level,
- Any rough terrain/sloping surface etc that the lifting equipment will need to travel on and,
- General accessibility of the site.
This is not an exhaustive list and individual site requirements must be considered in equipment selection.
The correct vacuum lifter must have multiple suction heads. The use of vacuum lifters with a single suction head is not recommended.
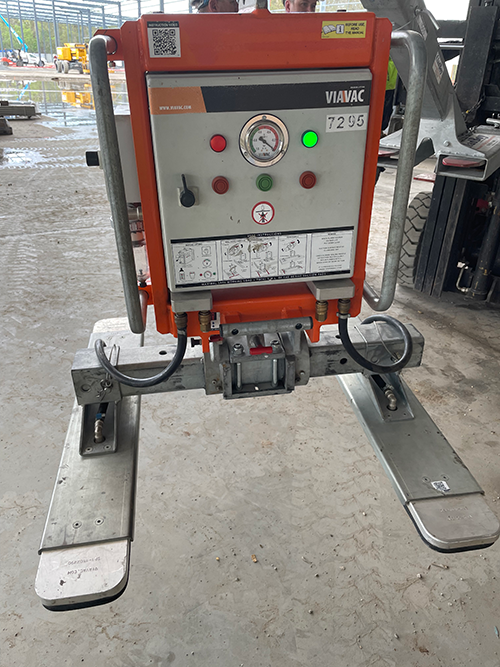
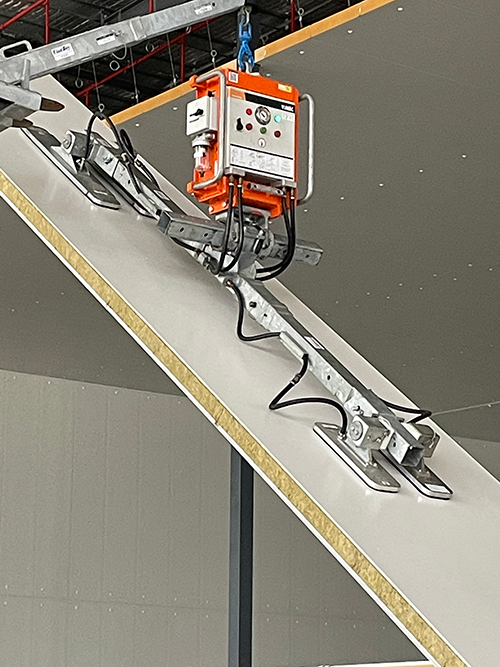
Once the correct vacuum lifter has been sourced and correctly located onto the MW panel one end of the panel must be slid slightly to one side of the remaining MW panels in the pack. The panel to be lifted with the vacuum lifter must then be manually lifted enough to break the suction between the MW panels before the vacuum lifter takes the panel weight.
Correctly locating of vacuum lifter on the panel
Correctly locating the vacuum lifter on the MW panel will help avoid damage to the panel.
The suction heads of the vacuum lifter should be located 70% of the length of the panel from what will become the bottom of the panel when the panel is in the vertical position.
When a vacuum lifter with extension arms is used the 70% distance is measured from what will be the bottom of the panel to what will be the lowest suction heads when the panel is in the vertical position.
Carefully conduct a test lift to confirm the vacuum lifter is in the correct location.
Jerking or sudden lifting of the vacuum lifter is to be avoided as this raises the risk of the top skin separating from the core of the panel.
Potential consequences
The key to the successful use of MW panels is to ensure the panel core remains completely dry and securely glued to the steel skins.
Incorrect handling or storage of MW panels can result in delamination or creasing of the panel.